Machining is the most important production method for processing metallic materials. The process is accompanied by a large number of interactions. In order to be able to understand and analyze these, they are mapped by machining experiments, thus generating a comprehensive under- standing of the process. Besides experiments, chip formation simulations have also become estab- lished. The advantages of simulation-based investigations are that the number of necessary tests can be reduced, the development time can be shortened and thus costs can be saved. For meaningful simulation results, it is crucial to represent the machined materials and their behavior under thermal and mechanical load as accurately as possible. This is realized by so-called material models. These models can guarantee a high representation of reality by the correct determination of the characteristic values.
The aim of this work is to provide an overview of the material models used in machining simulations and to present them in a comparative manner. Furthermore, it will be shown how the characteristic value determinations for the individual models are carried out and validated.
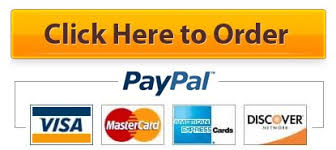